An inventory management system, well-tuned, will collect a lot of data. And what good are inputs if you don’t have great outputs? Using the data produced by your parts and material tracking system is critical to ensuring success. So today we want to talk about construction parts and materials dashboards and reports… ’ya know, the fun stuff!
This article is for those organizations who maintain an inventory of parts and/or materials within their organization.
Designing an “awesome” construction parts and materials dashboard is all about optimizing data for the areas of your organization you should be focusing on. And those areas you should be focusing on are those most responsible for delivering a return on your investments. I have worked with a lot of parts and materials managers who want to track activity that isn’t overly impactful. I would suggest your first and most important dashboard should focus on the money. In other words, what are those data points that impact the company’s bottom line the most. Typically, this includes 4 components:
- Consumption
- Aging
- Vendor Performance
- Operational Efficiency
Parts and Materials Consumption
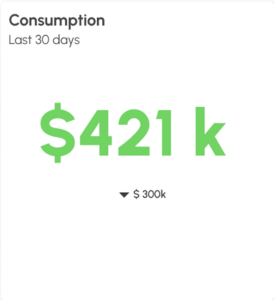
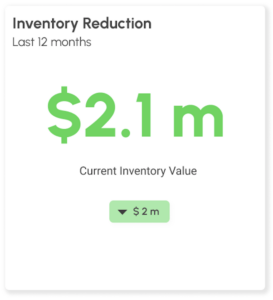
Of course, every good inventory management system should help you understand what you’re using, where, and how much is being used. Drilling down on the dashboard should tell you more about the parts and materials you’re using and help you to consider whether they’re being used as effectively as possible. On a month-to-month basis are material costs rising and lowering in line with your revenue? Are parts flowing to equipment in a way that makes sense based on your shop’s workload? Most importantly, is your total inventory on hand increasing or decreasing? It often only takes a small percentage decrease in inventory on hand to add significant cash availability back to the company.
Aging
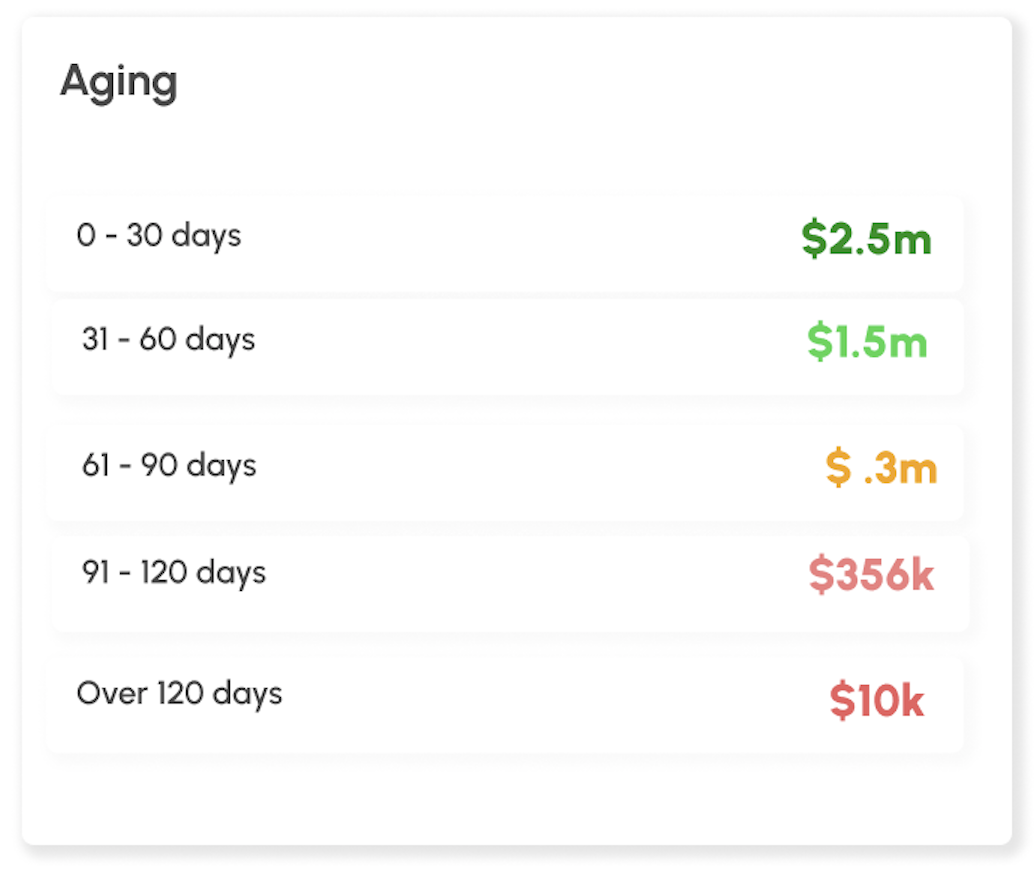
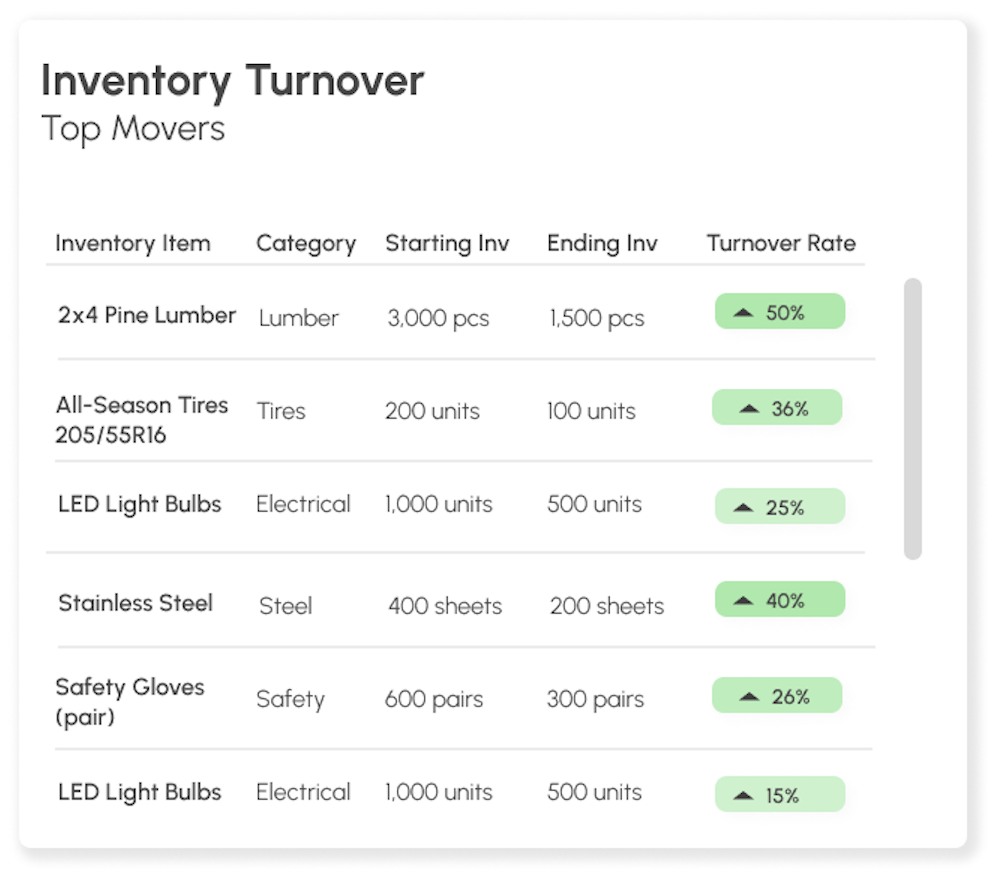
Everyone has a few things in their warehouse that have been there forever. But do you know the exact value of all the items which have been in your warehouse more than 120 days, or perhaps 6 months or more? Aging parts and materials can have a big impact on a company’s bottom line. Of course, it is important to have what you need when you need it. However, a team that over emphasizes availability will result in a warehouse full of unused inventory. It’s just as important to understand what’s sitting on the shelf for too long a period and how you might minimize that.
Vendor Performance
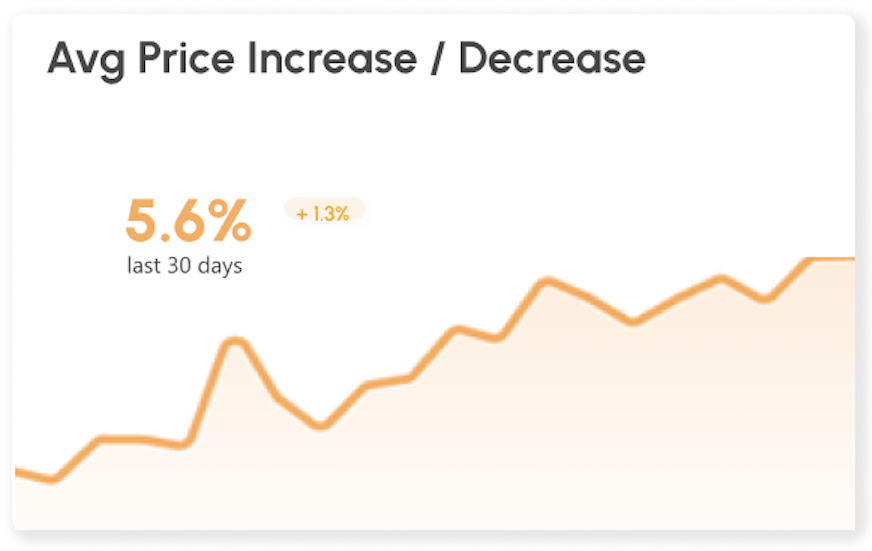
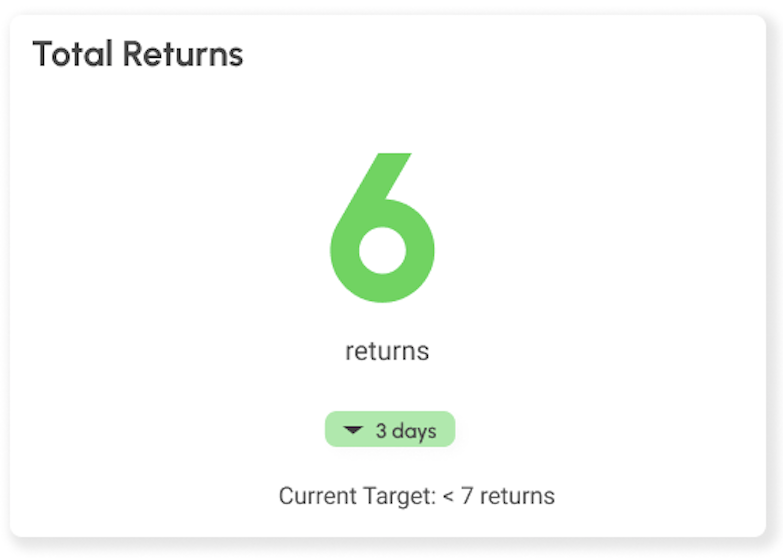
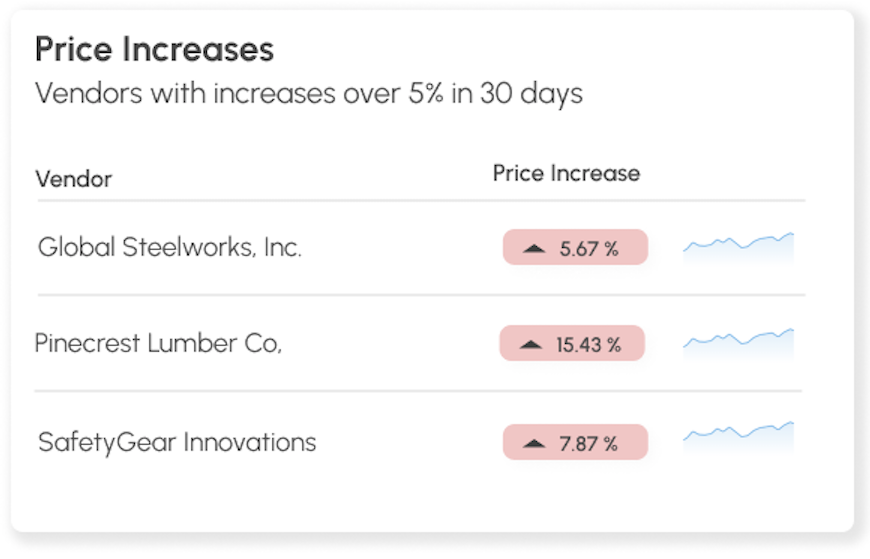
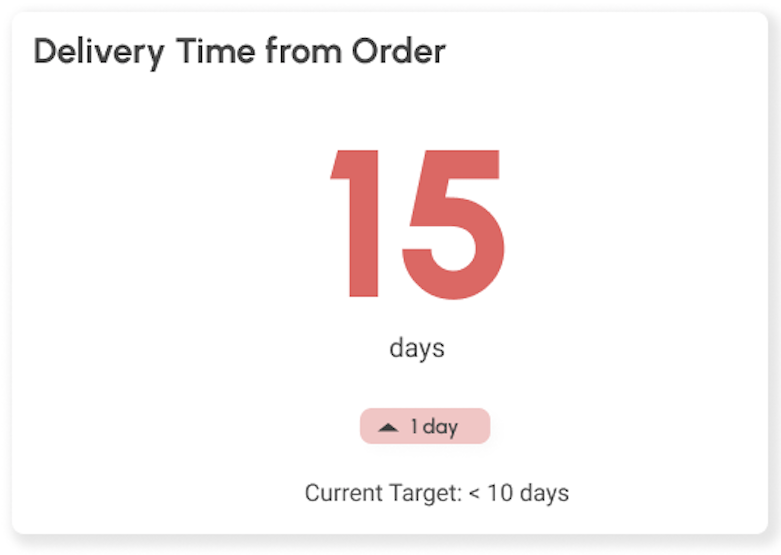
This is a big one that’s often overlooked or is simply too challenging to track. Understanding how you are really being treated by your vendors can be extremely powerful. Imagine showing your sales rep a report detailing their price increases compared to their competitor. But it’s not just pricing. Delivery and availability performance as well as order accuracy is also important to ensuring delays are minimized. A good inventory management system will include all the information you need to produce vendor scorecards to help identify your low and high performing vendors so you can pressure them to do better or move to a different supplier.
Operational Efficiency
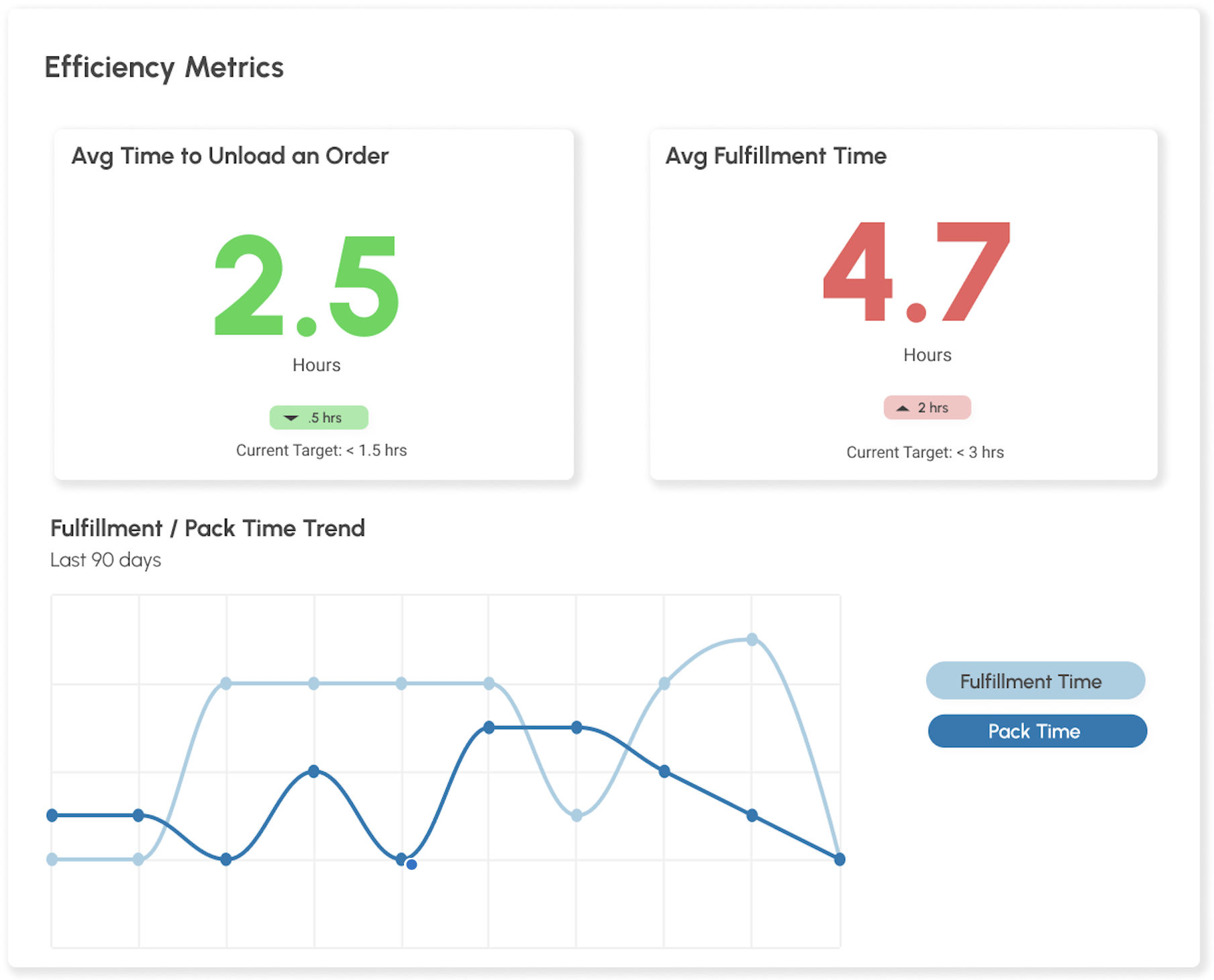
A good team is always striving to get better. But what exactly is “better”? A good parts and materials dashboard defines this for you and measures your progress. This is extremely important and potentially very motivating for the team (or demotivating for lower performers). Being able to track operational performance and provide the team with a pat on the back as efficiency improves can have a huge impact on retention, labor costs and more. Giving your leads better tools to measure the effectiveness of the changes they implement will encourage them to experiment and optimize even more. Such tools can also help you understand when the team is over-worked, and staffing levels may need to increase.
Summary
A good construction parts and materials dashboard is the gift that keeps on giving. It’s the key to unlocking financial return for your technology and operational investments. By focusing on those elements that reduce cost and increase efficiency you ensure operations are focused on the bottom line.